QHSE Consultancy Solutions
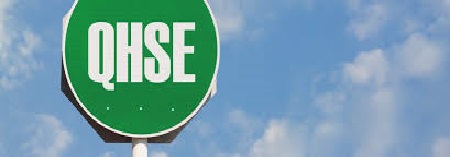
It’s the provision of auditing activities related to Quality, Health, Safety, and Environment (QHSE) management systems within organizations.
QHSE auditing involves the systematic examination and assessment of an organization's policies, procedures, processes, and practices to ensure compliance with relevant standards, regulations, and best practices in quality, health, safety, and environmental management. The primary objectives of QHSE auditing services include:
1. Compliance verification: Auditors assess whether the organization's QHSE management systems align with applicable legal requirements, industry standards, and internal policies.
2. Identification of gaps and non-conformities: Auditors identify areas where the organization's QHSE practices deviate from established standards or where there are deficiencies in implementation.
3. Risk assessment: Auditors evaluate the effectiveness of the organization's risk management processes in identifying, assessing, and mitigating QHSE risks.
4. Continuous improvement: Auditors provide recommendations for improvement based on their findings, helping the organization enhance its QHSE performance and achieve its objectives more effectively.
Overall, QHSE auditing services play a crucial role in helping organizations maintain high standards of quality, health, safety, and environmental performance, while also supporting continuous improvement efforts.
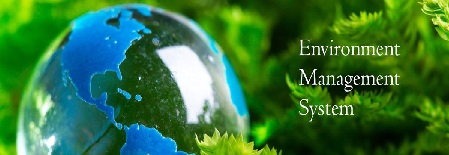
Environmental studies, specifically focusing on Indoor Environment Quality (IEQ), encompass the assessment and analysis of various factors that affect the quality of the indoor environment within buildings. IEQ refers to the overall condition of indoor spaces in terms of comfort, health, and productivity for the occupants.
Key aspects of Indoor Environment Quality include:
1. Air quality: This involves assessing the levels of pollutants, such as volatile organic compounds (VOCs), particulate matter, carbon monoxide, and other contaminants present in indoor air. Poor air quality can lead to respiratory issues, allergies, and discomfort for occupants.
2. Thermal comfort: Evaluating the temperature and humidity levels within indoor spaces to ensure they are within acceptable ranges for human comfort. Factors such as inadequate heating or cooling, humidity imbalance, and drafts can impact thermal comfort.
3. Lighting: Assessing the quantity and quality of natural and artificial lighting in indoor spaces. Proper lighting is essential for visual comfort, productivity, and mood regulation among occupants.
4. Acoustics: Analysing the levels of noise and reverberation within indoor environments. Excessive noise can lead to distractions, stress, and reduced productivity.
5. Ventilation: Evaluating the effectiveness of ventilation systems in providing adequate fresh air circulation and removing indoor pollutants. Poor ventilation can result in the buildup of indoor pollutants and discomfort for occupants.
Environmental studies focusing on IEQ typically involve field measurements, data collection, occupant surveys, and computer simulations to assess and improve the indoor environment. The goal is to create indoor spaces that promote health, comfort, and productivity while minimizing adverse effects on occupants and the environment.
Optimizing Indoor Environment Quality is essential for creating a conducive and healthy indoor environment for occupants. It can also contribute to energy efficiency, sustainability, and overall building performance.
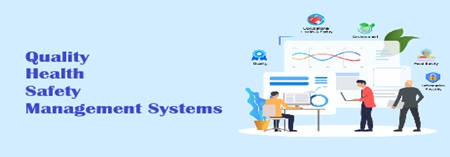
Quality, Health, and Safety Management Systems (QHSEMS) refer to integrated systems within organizations that are designed to ensure the effective management of quality, health, and safety aspects of their operations. We provide these management systems aims to structure the framework for establishing policies, procedures, processes, and controls to achieve and maintain high standards in these areas.
The components of QHSEMS are:
1. Quality Management: Quality management focuses on meeting customer requirements and delivering products or services that meet or exceed their expectations. Quality management systems (QMS) typically adhere to international standards ISO 9001. Key components of quality management include quality planning, quality control, quality assurance, and continuous improvement.
2. Health Management: Health management involves ensuring the well-being and safety of employees within the workplace. It includes identifying and mitigating occupational health hazards, promoting healthy work practices, providing health and wellness programs, and complying with health-related regulations and standards.
3. Safety Management: Safety management focuses on preventing accidents, injuries, and occupational illnesses within the workplace. It includes identifying and assessing safety risks, implementing safety procedures and controls, providing safety training to employees, conducting safety inspections and audits, and complying with safety regulations and standards.
Integration of Quality, Health, and Safety Management Systems:
We offer integrated quality, health, and safety management systems into a single, cohesive framework to streamline processes, reduce duplication of efforts, and enhance overall effectiveness. Integrated management systems help organizations achieve synergies between quality, health, and safety objectives, leading to improved operational efficiency and better outcomes for employees and stakeholders.
The implementation of QHSEMS is often guided by international standards which are ISO 45001 for occupational health and safety management systems, ISO 9001 for quality management systems, and ISO 14001 for environmental management systems. These standards provide a common framework for organizations to establish, implement, maintain, and continually improve client’s QHSEMS, leading to enhanced performance, customer satisfaction, and regulatory compliance.
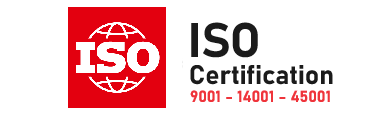
We help organizations achieve certification to ISO (International Organization for Standardization) standards. ISO standards are globally recognized benchmarks for quality, safety, efficiency, and environmental management systems, among other aspects of business operations.
ISO certification typically assist companies in understanding the requirements of specific ISO standards relevant to their industry and operations. We provide guidance on implementing necessary processes, documentation, and systems to meet these standards.
By following the below process:
1. Gap analysis: Assessing an organization's current practices against the requirements of ISO standards to identify areas that need improvement.
2. Documentation: Assisting in the development of necessary policies, procedures, and documentation to meet ISO standards.
3. Training: Providing training programs to educate employees on ISO standards and how to implement them effectively.
4. Internal audits: Conducting internal audits to evaluate compliance with ISO standards and identify areas for improvement.
5. Certification preparation: Guiding organizations through the certification process, including selecting an accreditation body, preparing for audits, and addressing any non-conformities.
ISO certification aims to streamline the certification process, enhance organizational efficiency, improve product or service quality, and enhance customer satisfaction.
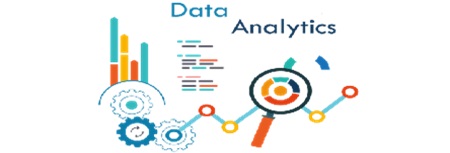
QHSE data analysis stands for Quality, Health, Safety, and Environment data analysis. We approach the process, examining and interpreting data related to various aspects of an organization's operations, specifically focusing on quality management, health and safety practices, and environmental performance.
In many industries, maintaining high standards in quality, health, safety, and environmental (QHSE) management is critical for ensuring regulatory compliance, reducing risks, and enhancing overall operational efficiency. QHSE data analysis involves collecting, organizing, and analysing data from different sources within an organization to gain insights into its performance in these areas.
1. Quality data: Information related to product or service quality, such as defect rates, customer complaints, and product/service performance metrics.
2. Health and safety data: Data concerning workplace accidents, near-misses, safety incidents, injury rates, and compliance with health and safety regulations.
3. Environmental data: Data on environmental impact, such as energy consumption, waste generation, emissions, and compliance with environmental regulations.
The goal of QHSE data analysis is to identify trends, patterns, and areas for improvement in quality, health, safety, and environmental performance. By analysing this data, your organizations can make informed decisions, implement corrective actions, and continuously improve their QHSE management systems to enhance overall effectiveness and sustainability. Additionally, QHSE data analysis plays a crucial role in reporting to stakeholders, regulatory authorities, and certification bodies.
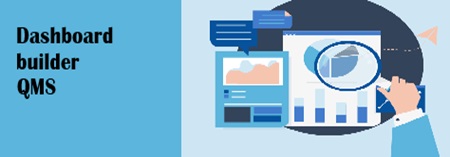
Building Quality, Health, and Safety (QH&S) dashboards involves the creation of visual tools or interfaces that provide real-time or near-real-time insights into various aspects of quality, health, and safety management within an organization. These dashboards consolidate key performance indicators (KPIs), metrics, and data from different sources to facilitate monitoring, analysis, and decision-making related to QH&S management.
The key components and objectives of building QH&S dashboards are:
1. Data Integration: QH&S dashboards pull data from multiple sources, including quality management systems (QMS), health and safety management systems (HSMS), incident reporting systems, environmental monitoring systems, and other relevant databases. Integration ensures that the dashboard provides a comprehensive view of QH&S performance across the organization.
2. Key Performance Indicators (KPIs): QH&S dashboards typically display a set of KPIs that are relevant to quality, health, and safety management. These KPIs may include metrics such as accident rates, near-miss incidents, compliance with safety regulations, customer satisfaction scores, product quality metrics, and environmental performance indicators.
3. Visualization: Dashboards use various visualization techniques, such as charts, graphs, gauges, heatmaps, and trend lines, to present QH&S data in a visually appealing and easy-to-understand format. Visualization helps stakeholders quickly identify trends, patterns, and areas that require attention or improvement.
4. Real-Time Monitoring: QH&S dashboards often provide real-time or near-real-time monitoring of key metrics and performance indicators. This allows stakeholders to promptly identify emerging issues, respond to incidents, and take proactive measures to address potential risks to quality, health, and safety.
5. Customization and Interactivity: Dashboards may offer customization options that allow users to tailor the display of data according to their specific needs and preferences. Interactivity features, such as drill-down capabilities, filtering options, and data exploration tools, enable users to delve deeper into the data and gain actionable insights.
6. Reporting and Analysis: QH&S dashboards facilitate reporting and analysis by enabling users to generate customized reports, export data for further analysis, and conduct ad-hoc queries. This supports data-driven decision-making and continuous improvement initiatives in QH&S management.
Overall, building QH&S dashboards enhances transparency, visibility, and accountability in quality, health, and safety management by providing stakeholders with timely access to relevant information and insights. These dashboards serve as valuable tools for monitoring performance, identifying areas for improvement, and driving organizational excellence in QH&S management.
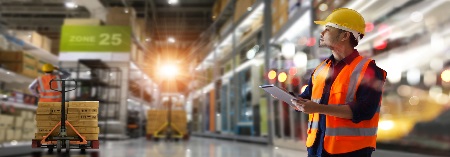
Risk assessment and risk management are essential processes for identifying, evaluating, and mitigating risks within organizations to ensure the achievement of objectives and the protection of assets.
1. Risk Assessment:
Risk assessment involves identifying, analysing, and evaluating potential risks that could affect an organization's ability to achieve its objectives. This process typically involves the following steps:
Identification of risks: Recognizing and documenting potential risks that could arise from internal or external factors, including strategic, operational, financial, and compliance risks.
Risk analysis: Assessing the likelihood and potential impact of identified risks on the organization. This step may involve quantitative analysis (using data and statistical methods) and qualitative analysis (based on expert judgment and risk criteria).
Risk evaluation: Ranking risks based on their significance, considering factors such as the likelihood of occurrence, potential impact, and tolerability thresholds set by the organization.
Our outcome of risk assessment is often documented in a risk register or risk matrix, which provides a comprehensive overview of identified risks and their characteristics.
2. Risk Management:
Risk management involves developing and implementing strategies to mitigate, transfer, accept, or avoid identified risks to reduce their potential impact on the organization. This process typically includes the following steps:
Risk treatment: Selecting and prioritizing risk response strategies to address identified risks. Common risk treatment options include risk avoidance (eliminating the risk), risk reduction (implementing controls to minimize the likelihood or impact of the risk), risk transfer (shifting the risk to another party, such as through insurance), and risk acceptance (acknowledging the risk and its potential consequences).
Implementation of controls: Developing and implementing control measures, procedures, and safeguards to mitigate identified risks effectively. This may involve improving internal controls, implementing safety measures, enhancing cybersecurity defences, or establishing contingency plans.
Monitoring and review: Continuously monitoring and reviewing the effectiveness of risk management strategies and controls to ensure they remain relevant and adequate. Regular reviews enable organizations to adapt to changing circumstances, emerging risks, and evolving regulatory requirements.
Effective risk assessment and risk management help organizations anticipate, manage, and mitigate potential threats and opportunities, thereby enhancing resilience, sustainability, and overall performance. These processes are integral components of good governance, strategic decision-making, and organizational success.
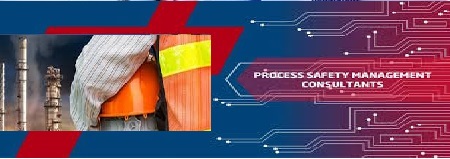
Our specialized experts help organizations to ensure the safe design, operation, and maintenance of industrial processes and facilities. Process safety focuses on preventing major incidents, such as fires, explosions, toxic releases, and other catastrophic events, that can result in loss of life, environmental damage, and significant financial losses.
The key aspects of process safety consultancy include:
1. Hazard Identification and Risk Assessment: Our consultants assist organizations in identifying and evaluating potential hazards associated with their processes, equipment, and operations. This may involve conducting hazard identification studies, such as Hazard and Operability Studies (HAZOP), Process Hazard Analysis (PHA), and Quantitative Risk Assessments (QRA), to systematically identify and assess risks.
2. Compliance with Regulations and Standards: Our consultants help organizations ensure compliance with relevant regulations, industry standards, and best practices related to process safety, such as OSHA Process Safety Management (PSM) regulations, EPA Risk Management Program (RMP) regulations, and international standards like API RP 750, API RP 751, and IEC 61511.
3. Safety Management Systems (SMS): We assist organizations in developing, implementing, and enhancing safety management systems tailored to their specific processes and operations. This may include establishing safety policies, procedures, and protocols, conducting safety audits and inspections, and providing safety training to employees.
4. Design and Engineering Support: We provide expertise in the design, engineering, and modification of process facilities to enhance safety and mitigate risks. This may involve reviewing process designs, recommending engineering controls and safeguards, and conducting process safety reviews of capital projects.
5. Emergency Preparedness and Response: Our consultants assist organizations in developing and implementing emergency response plans, procedures, and training programs to effectively respond to process safety incidents and emergencies. This may include conducting emergency drills, establishing communication protocols, and coordinating with emergency responders.
6. Continuous Improvement: We support organizations in implementing a culture of continuous improvement in process safety performance. This involves monitoring and analysing safety metrics, investigating incidents and near-misses, identifying opportunities for improvement, and implementing corrective actions.
Overall, process safety consultancy plays a critical role in helping organizations manage risks, prevent accidents, and ensure the safe and sustainable operation of their processes and facilities. By leveraging our expertise of consultants, organizations can enhance their process safety performance, protect their employees and assets, and maintain regulatory compliance.
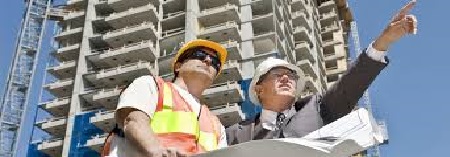
QHSE on-site survey and assessment involve conducting physical inspections and evaluations of your workplace or facility to assess its compliance with quality, health, safety, and environmental (QHSE) standards, regulations, and best practices. These surveys and assessments are typically carried out by our qualified QHSE auditors and consultants, who have expertise in evaluating various aspects of workplace operations.
The key components and objectives of QHSE on-site survey and assessment are:
1. Quality Assessment:
The quality assessment component focuses on evaluating processes, procedures, and practices related to product or service quality within the workplace. This may include assessing adherence to quality standards, customer requirements, and quality control measures.
2. Health Assessment:
The health assessment component involves evaluating factors that impact the health and well-being of employees within the workplace. This includes assessing potential health hazards, exposure to harmful substances, ergonomic factors, and the availability of health and wellness programs.
3. Safety Assessment:
The safety assessment component focuses on identifying and mitigating risks related to workplace safety. This may involve evaluating safety procedures, equipment, emergency preparedness plans, workplace hazards, and compliance with safety regulations and standards.
4. Environmental Assessment:
The environmental assessment component involves evaluating the environmental impact of workplace activities and operations. This includes assessing waste management practices, pollution prevention measures, energy consumption, emissions, and compliance with environmental regulations.
During the on-site survey and assessment process, Our QHSE professionals typically perform the following activities:
- Conducting physical inspections of the workplace, including equipment, facilities, and work areas.
- Reviewing documentation, records, and procedures related to QHSE management systems.
- Interviewing employees and management to gather information about QHSE practices and issues.
- Observing work practices and identifying areas for improvement.
- Identifying hazards, risks, and non-conformities related to QHSE standards and regulations.
- Providing recommendations and corrective actions to address identified deficiencies and improve QHSE performance.
The goal of QHSE on-site survey and assessment is to ensure that workplaces maintain high standards of quality, health, safety, and environmental management, thereby protecting the well-being of employees, minimizing risks, and ensuring regulatory compliance.
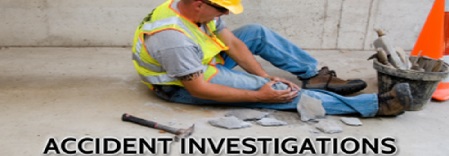
Accident/incident investigation services involve the systematic examination and analysis of workplace accidents, incidents, near-misses, or other adverse events to identify root causes, contributing factors, and lessons learned.
The key components and objectives of accident/incident investigation services are:
1. Immediate Response:
When an accident or incident occurs, the first step we ensure the safety of individuals involved and secure the scene to prevent further harm or damage. This may involve providing medical assistance to injured parties, isolating hazardous areas, and preserving evidence.
2. Data Collection:
Our investigators gather relevant information and evidence related to the accident or incident. This includes interviewing witnesses, involved parties, and stakeholders; collecting physical evidence; reviewing documentation, records, and reports; and examining the scene of the incident.
3. Root Cause Analysis:
Our investigators analyse the collected data to identify the underlying causes and contributing factors that led to the accident or incident. This may involve using techniques such as the "5 Whys" method, fault tree analysis, or fishbone diagrams to trace back the sequence of events and uncover systemic issues.
4. Report Generation:
Our investigators document their findings and conclusions in an accident or incident investigation report. The report typically includes a description of the incident, analysis of root causes, recommendations for corrective actions, and lessons learned. The report may also include a timeline of events, diagrams, photographs, and other supporting documentation.
5. Corrective Actions:
Based on the findings of the investigation, recommendations are made for corrective actions to prevent similar accidents or incidents from occurring in the future. These corrective actions may include implementing new safety procedures, improving training programs, modifying equipment or facilities, or addressing organizational and cultural factors.
6. Continuous Improvement:
Our Accident/incident investigation services aim to support a culture of continuous improvement in your workplace safety by identifying and addressing underlying causes of accidents and incidents. Lessons learned from investigations are used to enhance safety systems, practices, and processes to prevent future occurrences.
Overall, accident/incident investigation services play a critical role in identifying hazards, improving safety performance, and preventing accidents and injuries in the workplace. By conducting thorough investigations and implementing effective corrective actions, your organization can enhance safety culture, mitigate risks, and protect the well-being of their employees.
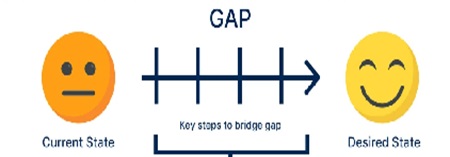
A Compliance Obligation Assessment and Gap Analysis (COAGA) is a process that needed to evaluate organizations compliance with legal, regulatory, contractual, and other requirements applicable to organizations operations. This assessment helps organizations identify any gaps or discrepancies between their current compliance status and the requirements they are obligated to meet.
The key components of a Compliance Obligation Assessment and Gap Analysis are:
1. Compliance Obligation Identification:
The first step involves identifying all relevant compliance obligations that apply to the organization. This includes laws, regulations, standards, permits, contracts, agreements, industry guidelines, and internal policies that govern the organization's activities.
2. Documentation Review:
Once the compliance obligations are identified, we review and gathers documentation related to these obligations. This may include statutes, regulations, permits, contracts, policies, procedures, and other relevant documents.
3. Gap Analysis:
The next step is to conduct a gap analysis to assess the organization's current level of compliance against the identified obligations. This involves comparing the organization's existing practices, processes, and controls with the requirements specified in the compliance obligations.
Gaps or discrepancies are identified where the organization's current practices do not fully meet the requirements of the compliance obligations. These gaps may relate to missing processes, inadequate controls, lack of documentation, or other deficiencies.
4. Risk Assessment:
A risk assessment will be conducted to prioritize and evaluate the significance of the identified gaps. This involves assessing the potential impact of non-compliance, including legal, financial, operational, reputational, and other risks associated with failing to meet the compliance obligations.
5. Action Plan Development:
Based on the findings of the gap analysis and risk assessment, an action plan is developed to address the identified gaps and achieve compliance with the obligations. The action plan outlines specific tasks, responsibilities, timelines, and resources needed to close the gaps and mitigate compliance risks.
6. Implementation and Monitoring:
We Monitor the organization implementation of the action plan and observe the progress towards achieving compliance with the identified obligations. This may involve implementing new processes, updating policies and procedures, providing training to employees, and establishing monitoring and reporting mechanisms.
7. Continuous Improvement:
Compliance is an ongoing process, so we help the organizations in continuously review and update their compliance programs to adapt to changes in regulations, business operations, and stakeholder expectations. Our support for the continuous improvement efforts is made to help ensure that the organization remains compliant and effectively manages compliance risks over time.
Overall, a Compliance Obligation Assessment and Gap Analysis enable organizations to identify, prioritize, and address compliance gaps, thereby reducing the risk of non-compliance and promoting a culture of compliance within the organization.