echo $menu_name; ?>
echo $name; ?>
Introduction
This course will provide a comprehensive review of the various aspects of engineered safety and mechanical integrity in refineries, oil and gas plants and petrochemical plants.
Principal emphasis is placed on the primary means of achieving plant integrity, which is the prevention of pressure equipment and piping failures, particularly, any which could cause significant consequences.
This course builds on a focused and practical coverage of engineering materials properties and the selection and provides structured procedures and applicable calculation formulae and methods for the mechanical design of process piping systems and pressure equipment.
The course underscores the importance of interactions and cooperation between the three key functions of engineering, operation, and maintenance in achieving the optimum mechanical reliability level in the plant. It enforces this key issue with practical examples of significant failures resulting from a lack of understanding of the roles, responsibilities, and interfaces between these functions.
Objectives
By the end of this course, participants will
- Understand and apply the various aspects of engineered safety to ensure mechanical integrity in a responsible and cost-effective manner.
- Gain enhanced knowledge and skills in hazard identification and analysis and in risk assessment and management.
- Learn practical and effective methods and tools to perform practical likelihood and consequence analyses.
- achieve measurable improvement in mechanical integrity through effective interaction between engineering, operation and maintenance functions
- Gain a sound working knowledge of the interdependence of design, operation, and maintenance on integrity, reliability, and cost-effectiveness of piping systems.
- Add to their ability and skills in piping failure detection and analysis, estimating failure consequences, and fitness for service assessment.
- Enhance their competence and productivity thereby enhancing their competence and performance level and making additional value-added contributions to their organizations.
Target Audience
This course is particularly valuable for refinery and petrochemical plant technical professionals, engineers, inspectors, maintenance personnel, as well as for project and consulting engineers and engineering and technical personnel involved in plant mechanical integrity and reliability.
echo $menu_name; ?> Outline
The course covers the following topics:
Technical integrity, industrial failures, and safety in design
- Technical Integrity An Overview
- Definition, scope, and key elements hardware and software issues, peopleware sound people management
- Potential threats to technical integrity in a hazardous environment
- Regulatory requirements
- Life cycle implications design/operation/maintenance, regulatory/industrial interface, training/staff development, networking
- Industrial Failures Catastrophic Failures Do Happen
- Statistics
- Typical examples
- Causes and implications
- Learnings
- Estimation of Consequences of Pressure and Storage Equipment Failures vessels, exchangers, heaters, storage tanks, and piping
- Types of Hazards release of hazardous substances, bleves, fractures, explosions, vapor cloud explosions
- Guidelines and Procedures for quantifying consequences
- Safety in Design I
- Project development and design bases
- Appropriate Codes, Standards, Specifications, Industrial Practices
- Safeguarding premises
- Calculation methods, heuristics
- Safety in Design II
- Quality Control in Design
- Inherent Safety
- Reliability and availability of premises
- Integration of operability and maintainability in the design
- Health, Safety and Environmental Considerations
- Roles and responsibilities of Engineering/Operation/Maintenance
- Operating Strategies Run Length, shifts
- Startup, Shutdown, Emergency Operating Procedures
- Steam out and Flushing procedures
- Isolation, blanking, vents, and drains
- The human factor: training modules, operator training
- Workshop 1 Failure Consequences Case studies and worked examples
Material selection and design of major equipment and piping systems
- Design Codes, Standards, Specifications, and Best Practices
- Fit for purpose facilities
- Business-focused facilities
- Liability and due diligence
- Engineering Materials I
- Types and application
- Imperfections and defects
- Specifications and standards
- Engineering Materials II
- The behavior of Metals Under Stress
- Degradation processes
- Selection methodology and guidelines
- Design of Major Plant Equipment Methodology and key considerations
- Pressure Vessels
- Heat Exchangers
- Fired heaters and boilers
- Design of Piping Systems I Pressure Integrity
- Methodology and key considerations
- Design of Piping Systems II Mechanical Integrity
- Special design considerations dynamic and transients loadings
- Piping flexibility and supports
Failures and failure prevention
- Safeguarding Systems I Guidelines and Best Practices
- Principles
- Guidelines and Best Practices
- Documentation
- Safeguarding systems integrity design
- Safeguarding Systems II Safety Systems Key Design Considerations
- Safeguarding safety systems SIL
- Relief and depressuring systems
- Safeguarding systems integrity and effectiveness
- Failures in Piping and equipment Pressure Vessels, Piping and Boilers
- Degradation processes
- Failures in pressure equipment
- Piping System Vibration and Failure
- Failures in Rotating Equipment
- Causes
- Monitoring and analysis
- Reliability improvement
- Failure Prevention
- Causal analysis
- Testing and Monitoring
- Inspection, Testing and Repair Regulations, Codes, and Practices
- Evaluation of Inspection Data
- Failures due to Improper Operation and Maintenance
Hazard and risk identification, assessment, and management
- Hazard Identification and Assessment
- Risk Analysis, Assessment, and Management
- Probability basics
- Probabilistic risk assessment concepts and methodology
- Fault tree and event tree analysis
- Quantitative risk assessment concepts and methodology
- Integrated Safety Management Plan
- Hazard and Effect Management Plan
- BowTie process
- Risk Matrix
- Determining acceptability of risk
- Hazard and Operability Reviews
- Process and guidelines
- Management of Change
- Change Control Policy and Procedures
- Process Changes
- Plant Changes
- Assessment and Authorization
- Documentation
- Illustrative Change Control Procedure
Operation and maintenance aspects of plant integrity
- Fitness For Service / Engineering Critical Assessments
- Fracture Mechanics and Mode of Failure of Material
- Flaw Characterization, Growth, Stability
- Factors of Safety
- Disposition versus Repair
- Maintenance Strategies and Programs
- Risk-based Inspection
- Reliability centered maintenance
- Rerating Piping and Pressure Vessels
- Engineering Information and Systems Management
- Troubleshooting Plant equipment and Piping systems
- Guidelines and best practices
- Resonance and Vibration
- Excessive Thrusts and Moments on Connected Equipment
- Leakage at Joints
- Excessive Piping Sag, Disengagement of Piping From Supports
- Interference With Expansion and Contraction
- Technical Integrity Audits
- Guidelines and procedures
- Checklists
- Implementation plans
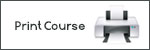
Ref | Location | From | To | Cost |
ME16 | Cairo | 27-12-2024 | 31-12-2024 |