Corrosion & Metallurgy
Metallurgy, Corrosion and Prevention of Failures
Introduction
Metallurgy: This section of the course presents a history of metals and the background on the origins of various metals. It provides an explanation of the physical characteristics of metals, including the reason metals behave differently than non-metals. This section of the course also explains how and why different metals are selected for specific environmental purposes, including resistance to wear, corrosion, heat, cold, repeated stress, and impact. This section of the course also deals with the metallurgical aspects of welding. Emphasis will be placed on mechanical metallurgy, material selection, and the fundamentals of welding technology, welding metallurgy, inspection and quality of welds.
Corrosion: This section of the course focuses on the fundamentals of corrosion as well as the potential problems caused by corrosion. It provides a review of the causes of corrosion and the methods for identification, monitoring, and control. An understanding of corrosion and its control is vital for any company hoping to avoid the high costs that can directly or indirectly attribute to corrosion. This section of the course also presents fundamental principles of corrosion and assists participants in recognizing corrosion problems, determining their causes, and understanding & selecting control methods. Emphasis is on the practical applications of corrosion technology to solve industrial corrosion problems.
Prevention of Failures: This section of the course focuses on the prevention of failures, the assessment of the state of damage in plant and equipment, and the use of failure analysis, inspection data, and operating history in predicting safe operating life or determining necessary remedial measures. Maintenance requirements, risk-based inspection (RBI) procedures, and the fitness for service (FFS) approach will be discussed along with the various mechanisms leading to damage and potential failure, mechanisms of accumulation, and predictive methods.
Objectives
By the end of the course, participants will be able to:
- Develop a good understanding of physical and mechanical metallurgy including crystal structure, phase diagrams, diffusion, phase transformations, and diagrams
- Conduct a review of nonferrous alloys and stainless steels
- Become familiar with the classification and heat treatment of steels
- Have a good background on metallurgy and ferrous metals
- Gain a deeper understanding of materials and metallurgy including the general characteristics of metals and alloys, and their mechanical properties
- Understand welding metallurgy, non-destructive examinations and the electrochemical principles
- Know the fundamentals of corrosion and identify its different forms in varying circumstances including atmospheric corrosion by water and steam
- Learn about passivity and passive films on stainless steels
- Improve knowledge on cathodic protection, protective coatings, and inhibitors
- Understand various aspects of high-temperature corrosion, prediction, and control
- Increase awareness on the different damage and failure mechanisms and be familiar with the methods of failure prevention and inspection
- Demonstrate preventative and predictive maintenance
- Recognize the OSHA requirements for mechanical integrity
- Appreciate and define the different API and ASME codes and standards related to the in-service, construction and repair
Target Audience
All personnel responsible for metallurgy, corrosion, or the prevention of failures in plant and equipment
- Inspection, metallurgy, and corrosion engineers
- Material engineers
- Design engineers
- Mechanical engineers
- Chemical engineers
- Corrosion field personnel
- Corrosion field technicians and supervisors
- Senior engineers and managers
- All engineers and technical staff whose responsibilities include the reduction of corrosion and the prevention of failure either at the design stage or during operation of the facility.
Corrosion & Metallurgy Outline
The course covers the following topics:
Introduction
Metallurgy
- Review of ferrous metals
- Glossary
Introduction to Steel
- Classification of steels
- Heat treatment of steels
Physical and Mechanical Metallurgy
- Crystal structure
- Phase diagrams
- Diffusion
- Phase transformations
Review of Nonferrous Alloys and Stainless Steels
- Aluminum
- Copper
- Nickel-based
- Stainless steel
- Heat treatment of nonferrous and stainless steels
Materials and Metallurgy
- Mechanical properties
- Metals and alloys
- General characteristics of metals
- Alloying
Welding Metallurgy
- Glossary
- Fundamentals
- Characteristics of weld solidification
- Weld microstructure
- Temperature changes in welding
- Residential stresses
- Welding processes
- Heat input
- Shrinkage and distortion in welding
- Weld defects
Non-destructive examinations
- Glossary
- Quality control
- Standards for NDT
- Welding
- Inspection techniques
Electrochemical Principles
- Glossary
- Overview
- Anodes and cathodes
- Electron flow
- Electrolytes
Forms of Corrosion
- General corrosion
- Localized corrosion
- Galvanic corrosion
- Dealloying
- Intergranular corrosion cracking
- Stress corrosion cracking
- Velocity effects
- High-temperature corrosion
Passivity and Passive Films on Stainless Steels
- Review of fundamentals
- Passive films
Corrosion by Water and Steam
- Role of contaminants
- Types of water
- Corrosion materials
- Cooling systems
- Water treatment
Atmospheric Corrosion
- Types of corrosion
- Change of environment
- Design considerations
Cathodic protection
- How cathodic protection works
- Galvanic anodes
- Impressed current systems
- Design of galvanic system
Introduction to Protective Coatings
- Coating fundamentals
- Types of coatings
- Surface preparation
- Cathodic protection
- Application and cure
- Specifications
Inhibitors
- Types of inhibitors
- Aqueous systems
- Other considerations
High-Temperature Corrosion
- Overview
- Prediction and control
- Damage and Failure Mechanisms
- Ductile and brittle fracture
- Failure mechanisms
- How components fail
Failure Prevention
- Introduction
- Failures and inspection
Prevention and Predictive Maintenance
- Process safety management
- Occupational health and safety
Mechanical Integrity
- Risk-based inspection
- Failure analysis
- Summary
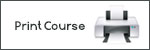
Ref | Location | From | To | Cost |
CM05 | Kuwait | 11-7-2021 | 15-7-2021 |